How to improve humidity measurements in extremely dry environments
Experiments
To demonstrate the problem and study its impacts, we built a test set-up (demonstrated in figure 1). The basic idea in the set-up was to have constant humidity, which was then disturbed by changing the temperature of tubing across a range from 20 °C to 27 °C. In theory, this would result in an adsorption/desorption effect, which influences the total amount of water vapor exiting the heat chamber. Similarly, a sampling tube out from the field to the measurement laboratory could be exposed to outdoor weather and thus to temperature changes. On a smaller scale, the varying indoor temperatures could impact similarly. During the experiments, gas pressure was kept within a range of 1 bar(a) to 2 bar(a) and the flow rate was at all the times less than 1 l/min, which corresponds with the flow rates of analyzers.

The set-up was comprised of a humidity generator, two Vaisala DMT152 dew point instruments, a heat chamber with a 6.7 m electropolished steel tube, and a CRDS analyzer. A DMT152 dew point instrument was placed before and after the heat chamber (Figure 1). Tubing from the second DMT152 to the analyzer was kept as short as possible to minimize ambient effects between the DMT152 and the analyzer. The temperature of the heat chamber was monitored with two temperature sensors.
Results
Multiple measurements were performed with different pressures, flow rates, and humidity. The heat chamber was controlled the same way through each of the experiments. (See Figure 2.)
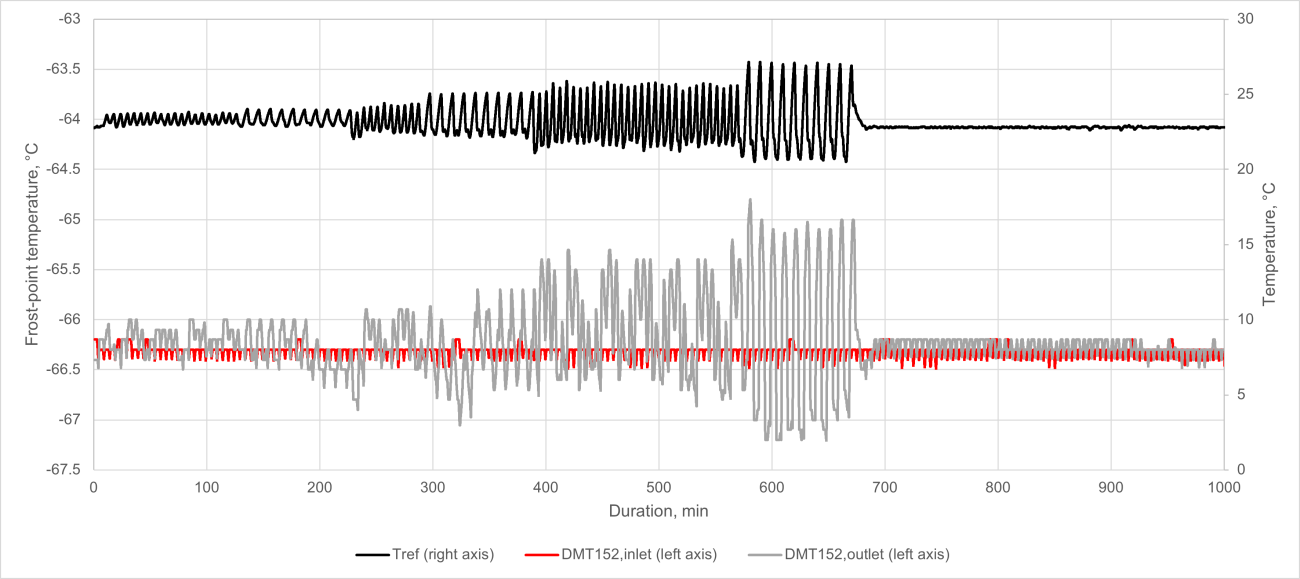
In Figure 2, as the temperature (black) is disturbed more and more, the more the DMT152 at the outlet detects noisy humidity while the inlet humidity is constant through the measurement. At the end of the measurement, the temperature is stabilized to laboratory temperature and both DMT152 instruments are again stable and indicate the same frost point temperature. This picture clearly demonstrates the effect of sampling tube temperature stability on output humidity - and hence to humidity measurements.
Another measurement is drawn in Figure 3. Here, inlet humidity was not as stable as in Figure 2, but both DMT152 instruments and the CRDS analyzer indicate a similar trend. However, in Figure 3 the inlet humidity is much less noisy in comparison to the CRDS analyzer or the DMT152 at the outlet. In fact, humidity at the outlet changes so much that neither the DMT152 nor the CRDS analyzer indicates the correct inlet humidity, and in fact, both are out of their specs. However, here the instruments are fully functional, and their performance is known to adhere to their specs; the problem is with the sampling tube. The changing temperature causes an adsorption/desorption phenomenon which results in varying humidity in the outlet of the sampling tube.
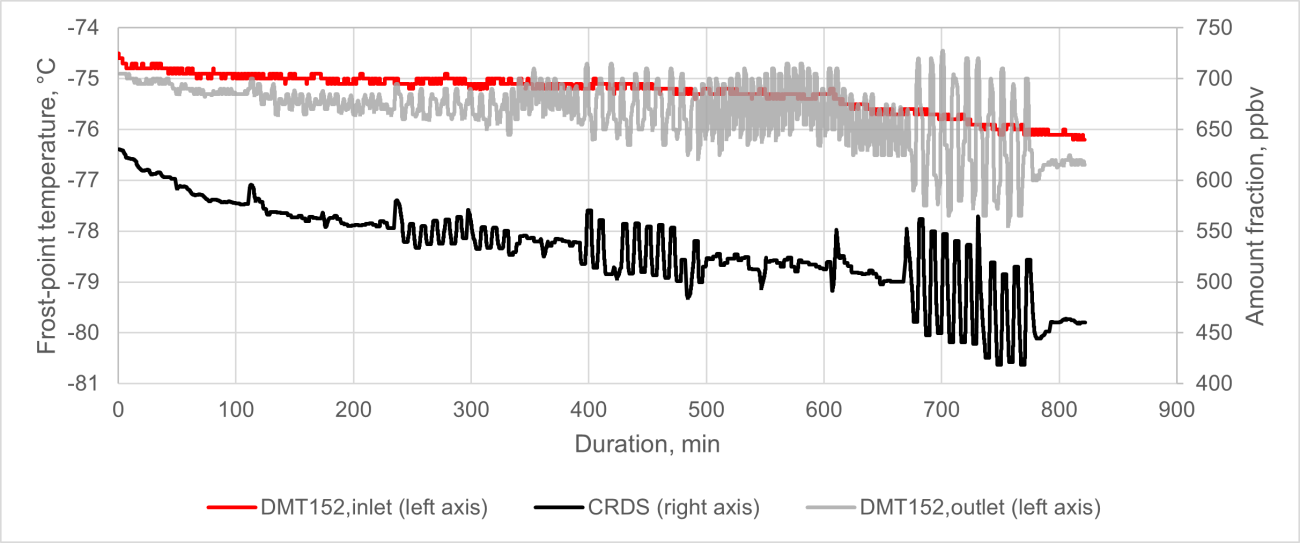
Results of the measurement campaign indicated:
- Maximum frost-point temperature change caused by adsorption/desorption was over 4 °C.
- Flow rate impacts: greater flow, bigger noise.
- The more temperature changes, the bigger the adsorption/desorption effect in tubing.
- The lower the humidity is, the greater the relative effect is.
Key takeaways
In this article ambient effects to sampling were tested. If the measurement environment or sampling is not ideal, it may have a significant impact on the measurement results. As shown in Figures 2 and 3, the more affordable DMT152, located at the inlet, outperforms the pricier analyzer thanks to the better representativity of the inline process measurement. Therefore, it is recommended to conduct measurements directly at the spot of interest and minimize the use of sampling whenever possible. This approach is also significantly more cost-efficient, thanks to the simpler measurement set-up and measurement principle.