Optimized drying process helps Isolava cut energy consumption and improve end-product quality
Isolava, founded in 1963 and part of Knauf group since 1990, manufactures gypsum plaster blocks for the construction industry. The most energy intensive part of the production process is drying, where the wet blocks are loaded into carts and carried through a four-stage drying oven. Process control has traditionally been solely in the hands of thermometers – until now.
In late 2017, Isolava began a project to optimize the drying process, led by Project Engineer Peter Vaneyghen. The first step was to install humidity sensors in the dryer in order to get a better understanding of the dynamics of the drying process.
Understanding a complex process
The goal of any industrial drying process is to ensure that the moisture level of the product is as uniform as possible. In order to optimize the drying process, it was crucial for Isolava to understand the drying dynamics of gypsum blocks – but there is no easy and reliable way to measure the moisture content of a gypsum block until after drying is completed.
Drying a solid material is a mass transfer process, meaning that the moisture evaporates from the object to the surrounding environment. The environment inside the oven is controlled using gas burners to generate warm air, ventilation to remove excess humidity, and fans to circulate the drying air evenly between the product surfaces. The process starts by warming up the products to oven temperature. Next is the constant rate phase, where the material contains so much water that there is a liquid surface. Finally, during the falling rate phase, there is no free moisture left on the product surface and the movement of moisture from within the material to the surface dries the product.
In addition to having the typical drying mechanism of a hygroscopic product, gypsum has another variable that must be taken into account: it consists of different salts, some of which are water soluble. During the process, the dissolved salt is transported to the surface of the block, where it crystallizes when the water evaporates.
“We studied the microstructure of the dried blocks using an electron microscope and found out that uncontrolled drying in the early stages of the process may lead to a lower drying rate in the later stages, when the capillaries of the material are closed,” explains Vaneyghen.
“In addition to a lower drying rate, this can also be observed as discoloration of the product,” he continues.
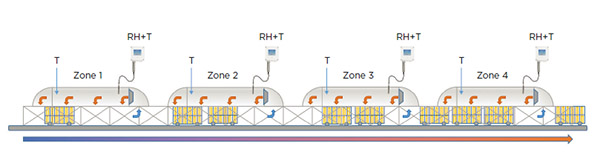
Savings through optimization
“By drying less in the early stages of the process and controlling the water reduction, we found we can modulate the last drying stage and minimize moisture variation in the final product. In light of this, a new, advanced control scheme was implemented by measuring the temperature and humidity,” Vaneyghen explains.
The results are impressive: the consumption of natural gas alone has decreased by some 20% and the annual savings across all ten dryers add up to hundreds of thousands of euros. In addition, the final moisture level in the finished product has been stabilized despite the speed variation in how fast blocks travel through the dryers.
“Drying is an interesting and intriguing topic for me. Finding a working solution that has been sought for a long time is rewarding. However, this requires intensive and in-depth work.”
Vaneyghen also points out that the right instrumentation has played a significant part in the success of the new solution. Currently, the Wielsbeke plant is running 40 Vaisala HMP7 humidity and temperature probes with Indigo201 transmitters.
“From a serviceability point of view, the interchangeability of the probe is a big advantage. If a sensor needs to be calibrated, it can be easily changed without disconnecting the transmitter.”
An ongoing project
The next step is to optimize the drying of Isolava’s drywall board products, and Vaisala's high temperature tolerance dew point transmitters are currently being tested for this purpose.
“This process involves a long time between the initial and final material moisture measurements, which makes it challenging from a control point of view,” Vaneyghen explains.
“We are incorporating machine learning and dew point measurements for improved control of board drying.”
Indigo compatible smart probes for this type of a drying process
Vaisala HUMICAP® HMP7 is an interchangeable humidity and temperature probe with Modbus RTU output, and is compatible with Vaisala Indigo series transmitters. The probe includes the latest-generation Vaisala HUMICAP® R2 sensor, which provides excellent accuracy and long-term stability and can tolerate temperatures of up to 180°C.
Vaisala DRYCAP® DMP6 is designed for humidity measurement in industrial drying applications in with very high temperatures up to 350°C. High temperature tolerance is achieved using a passive cooling set that conducts heat away from the probe and reduces temperature to optimal range for the sensor.