Old Cooling Methods Benefit from Using New Technology
Cooling tower control systems depend on accurate and reliable humidity measurement to increase energy efficiency and reduce maintenance costs.
Cooling towers are among the oldest and most effective methods of removing heat from a building. Unfortunately, tradition can lead operators to use familiar but unreliable
devices that result in inaccurate relative humidity (RH) measurements that compromise tower efficiency. Adopting advanced technology for accurate and reliable RH and temperature
measurements is essential for lowering energy use and maintenance costs.
Purpose is to Remove Heat
In HVAC applications, evaporative cooling towers remove heat from the condenser water – water used to cool the refrigerant – in chillers of HVAC systems. During this refrigerant-to-water heat exchange, the refrigerant temperature decreases and the condenser water temperature increases. The heated condenser water is then circulated to the cooling tower, where it is sprayed or splashed onto complex ventilated surfaces, maximizing evaporation that removes heat from the water. The cooled condenser water is then returned to the chiller to continue the cycle.
Wet-bulb Temperature Sets Cooling Limit
How much the condenser water can be cooled is limited by tower design, tower quantity, operating equipment including fans and pumps, and by environmental factors – it can be
cooled only as low as outdoor wet-bulb temperature, a function of RH and temperature. In a perfectly efficient cooling tower, the water leaving the tower is as cold as the wet-bulb temperature. Since no tower is perfectly efficient, tower designers consider its limitations to determine the approach – the approach is the practical difference between the possible and realistic temperatures of water leaving the tower.
The approach is added to the wet-bulb temperature to determine the actual condenser water setpoint. For example, 21°C (70°F) wet-bulb temperature with 4°C (7°F) approach
results in an actual setpoint of 25°C (77°F) for condenser water discharged from the tower. “Wet-bulb temperature measurement is similar to a temperature gauge in your car. It tells you how hard you can run the engine,” says Tim Wilcox of WPI, a U.S.-based consulting firm specializing in energy efficiency on a broad range of projects. “Its information is also used like the speed governor to avoid overrunning the equipment. Inaccurate measurement in either case can do great harm,” he adds.
Sources of Error
Inaccurate RH sensors are a common source of erroneous wet-bulb temperatures, misleading control systems and operators. Another source of error is locating the RH sensor too
close to the cooling tower, where it is affected by discharge air. Since the wet-bulb measurement must be true measurement of the outdoor ambient air, the RH device needs to be located away from any discharge air. “If the control systems are receiving a wet-bulb reading much cooler than possible, the operating engineers or the controls will attempt to
drive down the condenser water temperatures by engaging more pumps, fans and tower cells. The hardware can’t achieve the bogus temperature but the false information will
waste energy and risk fouling – if not harming – the cooling towers. A second-rate RH device will lead to an impossible condition,” Wilcox says.
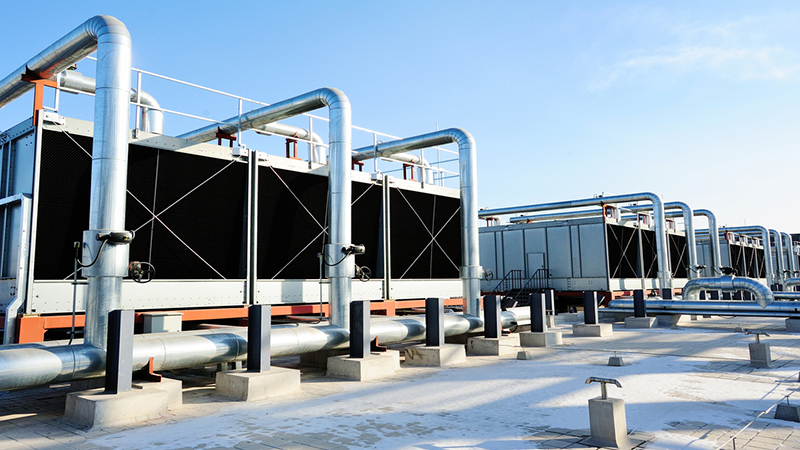
Costs of Overrunning
Excessive operation leads to several areas of avoidable operational and capital costs: wasting energy to run the fans more than needed, premature equipment repair, acceleration
of mineral build up in the tower fill, and inefficient water use from adding more water to the sump to replace the evaporated water. In one case that Wilcox cites, investigations concluded that inaccurate readings from an on-site RH device contributed to a cooling tower at a landmark hotel being so excessively run that the tower fill became nearly rock solid with calcium carbonate deposits. Uneven air flow rising through the plugged fill caused the tower system to be on the verge of shaking apart, damaging the fans and fan shrouds. Operators used fire hoses to keep the chiller plant operating at the height of the summer tourist season. Avoidable capital costs added up to hundreds of thousands of dollars to replace the tower fill.
Vaisala Recommended “Humidity measurements need to be accurate and maintainable. We specify Vaisala humidity sensors that we can count on not to migrate into error. We avoid recommending instruments that can go out of calibration in six months, misinforming the control systems and building operators,” says Wilcox. “We see projects that can spend
$200,000 a year on cooling tower related operating costs operated by a $50 sensor that goes unreliable in months. Life is too short to deal with error-prone devices.”
The Vaisala Humicap® HMT330 Series Humidity and Temperature Transmitter delivers high accuracy and excellent long-term stability, even in harsh outdoor conditions. RH accuracy is within 1% up to 90% RH and within 1.7% up to 100% RH. Temperature accuracy is within 0.2°C (0.36°F). The transmitters calculate wet-bulb temperature and can be field calibrated to meet the operator’s quality management protocol.
Accuracy Leads to Free Cooling
Wilcox recently reviewed cooling tower performance at an undisclosed data center in Utah. One of the recommended upgrades was to replace their RH device with the more accurate
Vaisala instrument. Now using accurate RH in the wet-bulb temperature measurement, the facility could reduce energy costs by using more free cooling. Free cooling can be used when the outdoor wet-bulb temperature plus the approach is lower than the requirement for primary chilled water. Under these conditions, the condenser water cools the primary
chilled water, bypassing the chiller entirely. Free cooling reduces mechanical cooling costs, is more energy efficient, and is recognized as a green energy effort. With accurate wet-bulb temperature measurements, the data center was able to convert to free cooling for more than half the year and still meet its cooling requirements.
New Ways are Better
The value of accurate RH measurements is increasing as more cooling tower builders, operators, and HVAC professionals learn – still too often the hard way – that more reliable
sensors using advanced technology can pay for themselves many times over.
Add new comment