Hydrogen production is a large and growing industry. The hydrogen economy is proposed to be a big part of the future low-carbon economy, which would eventually phase out fossil fuels as our primary energy source and mitigate global warming. One of the main benefits of hydrogen is its suitability for a wide range of fuel cell applications.
The applications where fuel cell technology is used can be divided into three main categories: portable power generation (for mobile devices and portable auxiliary power), stationary power generation (distributed power generation, back-up power sources, and grid-connected power stations), and transportation (cars, public transportation, and heavy machinery). One of the key drivers of market growth is the automotive industry, which is conducting intensive research aimed at pushing fuel cell technology in the automobile market.
Operating principle
Fuel cells convert chemical energy directly into electrical energy without any combustion process. The operating principle of the fuel cell is based on reduction-oxidation reactions. The energy is released in reactions taking place between hydrogen and oxygen. This direct process has the advantage of high energy efficiency - over 50%, and even as much as 85% if by-produced thermal energy is also recovered. In terms of electricity production, this is beyond the efficiency of any combustion process.
Other benefits include zero emissions at the operating site and silent operation. The numerous different fuel cell technologies each have their own strengths and weaknesses. The three main technologies on the market today differ by the proton carrier medium: Polymer Electrolyte Membrane (PEM), Solid Oxide (SO), and Molten Carbonate (MC). Of these, PEM technology is the most versatile in terms of application due to its low operating temperature (<100 °C), which makes it equally suitable for use in small and large-scale fuel cells. Solid oxide fuel cells involve high temperatures and are best suited for larger scale applications, such as distributed power generation. Whereas PEM fuel cells use pure hydrogen, SOFC fuel cells may use natural gas or other hydrocarbons, from which the hydrogen is extracted in the reforming process. The high operating temperature of SOFC fuel cells makes it easier to integrate the reforming stage into the fuel cell device.
The operating principle of a PEM fuel cell is described in Figure 1. When the hydrogen fuel is split into protons (hydrogen ions) and electrons at the anode, the electrons are transported to the cathode over an external circuit, which generates an electrical current. The positive charge carriers (hydrogen nuclei) are transported through the moist membrane on the cathode, where their reaction with oxygen forms water. This reaction produces electricity and heat.
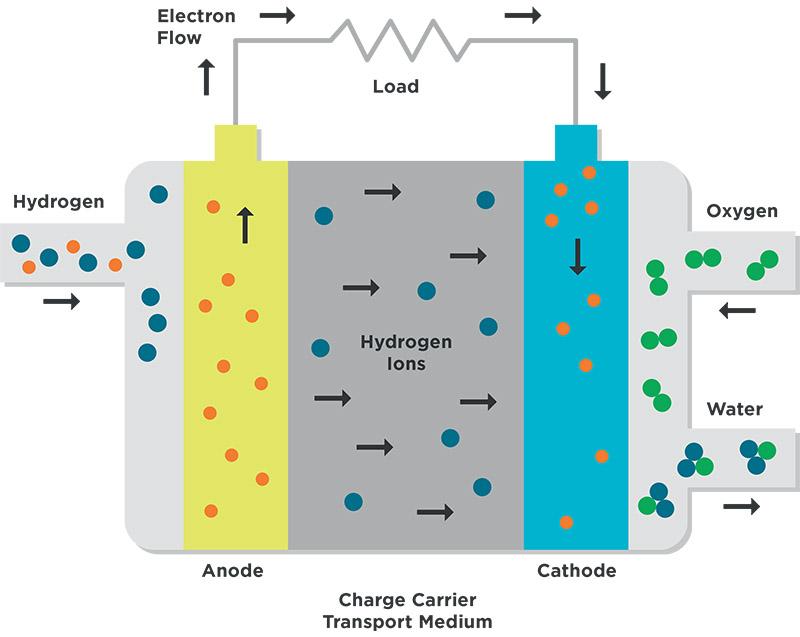
Figure 1: Operating principle of a PEM fuel cell. Hydrogen fuel reacts at anode in the presence of catalyst, forming electrons and hydrogen nuclei. These nuclei are transported to the cathode through a charge carrier medium where they react with oxygen to form water. Electrons travel through the external circuit, creating electric current.
Maximizing the efficiency of a fuel cell
Fuel cell efficiency is limited by different sources of loss: activation losses dictated by the catalytic reaction and condition of the catalysts, ohmic losses taking place in the transport medium during proton transportation, concentration losses due to limited mass transfer speed to reactive surfaces, and internal currents that occur when fuel is diffused through the membrane without reacting. The mechanisms behind the losses are related to water and temperature management in the cell. If temperature and moisture are not well controlled, aging of the catalysts and proton transporter medium increases losses, decreases the efficiency, and eventually leads to destruction of the cell.
Smaller PEM cells do not usually require humidification, but in larger cells carrying higher currents, the polymer membrane may need reactant humidification to prevent it dehydrating under load. The proton exchange capacity is directly proportional to the polymer moisture, and dry polymer will limit the reaction speed and cause losses in the cell.
Another consideration relating to dry polymer is its lifetime, which is one of the main concerns when fuel cells are designed. On the other hand, if the formed water is not removed sufficiently from the cathode side of the cell, water flooding leads to non-optimal operation of the cell. Humidity measurement in the fuel stream helps to control the humidification process, estimate mass balances for water, and maintain correct membrane moisture.
In order to improve reaction efficiency, abundant amounts of reaction gases may be led to the catalytic surfaces. Humid, unreacted fuel from anode outlet may be recirculated back to anode inlet to humidify the fuel stream. This recirculation may cause contaminant build-up, which is especially harmful in the case of PEM fuel cells.
In addition to fuel stream humidity control, humidity measurements in anode and cathode streams can be utilized in impurity measurements – when total pressure and partial pressures of hydrogen and water are known, the partial pressure of impurities in the circulation can be estimated.
Warmed probe technology helps to overcome the measurement challenge in high-humidity environments
Humidity measurements in fuel cell applications are performed in a high-humidity environment, typically over 80% relative humidity. Performing humidity measurements in near-condensing environments is a challenging task, as condensation may saturate the relative humidity sensor. Drying and recovery of the sensor may take a long time, and during that time the measurement is unavailable and the fuel stream moisture cannot be controlled.
Vaisala warmed probe technology offers a way to overcome this challenge since relative humidity can be reduced below condensing level by warming the sensor element above ambient temperature. With an additional temperature sensor located near the humidity sensor, the actual process temperature can also be measured. Combining these two values allows actual relative humidity in the high-humidity process to be calculated, and prevents the condensation problem at the same time.
VTT, one of the leading research organizations in Finland, is conducting both low temperature (PEM) and high temperature (SOFC) fuel cell research. VTT is utilizing Vaisala HMT310F and HMP7 humidity instruments, as well as GMP343 CO2 transmitters in their fuel cell related research.
“Vaisala humidity sensors are in active use in our research. Knowing the humidity of the reactant gases is crucial with both the low and the high temperature fuel cells”, says Mikko Kotisaari, Research Scientist, Fuel Cells, at VTT