As the world continues to move away from fossil fuels, the demand for high-quality batteries is rising. Batteries play a key role in electric vehicles and renewable energy storage, both of which offer environmental benefits. In this article we’ll look at how recycling N-Methyl-2-Pyrrolidone (NMP) can make battery manufacturing more sustainable – and bring cost savings too.
Expert article
Making battery manufacturing greener and more cost-effective – the role of NMP recycling

Maria Nyman
Product Engineer
Vaisala
The role of NMP in lithium-ion battery manufacturing and why recovery matters
N-Methyl-2-Pyrrolidone (NMP) is widely used as a solvent in lithium-ion (Li-ion) battery manufacturing to dissolve binders like polyvinylidene fluoride (PVDF) in electrode slurry preparation. The uniform slurry – containing NMP, binder, active material, and additives – is applied as a coating onto the electrodes at the core of high-performance batteries.
While NMP is essential to the many battery manufacturing process, it comes with challenges in terms of cost, environmental impact, safety risks, and compliance with regulations on solvent emissions. These challenges make proper handling and efficient recovery essential for reducing costs, minimizing emissions, and ensuring a safer workplace.
As battery manufacturers look for more sustainable and cost-efficient production methods, interest in optimizing NMP recovery is on the rise. The more NMP that can be recovered, the lower the production costs and the smaller the environmental footprint. Recovered NMP is often sold to recycling plants, which may supply it back to battery manufacturers. NMP can also be used in other sectors, such as the pharmaceutical and semiconductor industries.
By recovering and reusing NMP, manufacturers not only cut costs but also contribute to a more sustainable and responsible battery manufacturing process.
Optimizing NMP recovery
During the drying stage in battery manufacturing, NMP evaporates as part of the electrode slurry drying process. The NMP vapor released during the drying process is captured and purified through three main stages:
- Condensation: NMP vapor is captured, cooled, and condensed into liquid form. The liquid NMP is collected for further purification.
- Scrubbing: The remaining NMP vapor continues to a scrubber, where contaminants and residual gases are removed.
- Distillation: The purified NMP is distilled, separating the high-purity solvent from any remaining impurities and making it ready for reuse.
How inline refractometers help to optimize NMP recovery
Inline refractometers help make the NMP recovery process more efficient and therefore more cost effective. Continuous, real-time NMP concentration measurements enable precise control over key stages in the NMP recovery process. This allows immediate adjustments to be made, optimizing process performance and maintaining NMP quality.
There are two main areas where inline concentration measurements with inline refractometer technology help to optimize NMP recovery:
- The scrubber: Inline refractometers provide real-time concentration data, enabling precise adjustments to be made to scrubber parameters. This optimization reduces solvent loss, enhances recovery rates, and lowers production costs while minimizing water and energy consumption for more sustainable operations.
- The distillation column. Monitoring NMP concentration at the distillation column outlet ensures efficient energy use, enables fine-tuning of distillation parameters, and guarantees high NMP purity, preventing contamination in the recovered solvent.
Vaisala Polaris™ inline refractometers are ideal for real-time monitoring of NMP concentration. Both the Polaris™ PR53GC Compact Refractometer and the Polaris™ PR53GP Probe Process Refractometer can be paired with the Indigo520 Transmitter for easy and accurate real-time monitoring.
The environmental benefits of reducing solvent use and waste
Optimizing the amount of NMP used in battery manufacturing and reducing NMP waste helps to reduce the environmental impact of the manufacturing process. By recycling and reusing NMP, manufacturers can prevent it from being released into the atmosphere, which reduces air pollution, and minimize the risk of NMP contaminating water sources. Recycling and reuse also reduces the need to produce fresh NMP, which is an energy-intensive process. This helps reduce the carbon footprint of the whole battery production industry. Recycling NMP also helps manufacturers to comply with increasingly strict environmental legislation.
The economic advantages of recycling NMP and reducing raw material costs
In addition to the clear environmental benefits, there are several economic advantages associated with recycling NMP and reducing raw material costs. NMP is an expensive chemical, so optimizing its usage and recycling it wherever possible will reduce overall material costs. Reducing the demand for NMP also improves supply-chain resilience and reduces the risk of supply shortages. Finally, embracing the circular economy by recycling NMP can enhance a manufacturer’s brand reputation, while regulatory incentives and government grants for sustainable practices can also reduce operational costs.
Making battery manufacturing more sustainable
By reducing waste, lowering emissions, and recovering a valuable raw material, battery manufacturers can not only minimize their environmental impact but also enjoy substantial economic benefits. The best way to do this is with real-time monitoring of NMP concentration with inline refractometer technology. This helps to optimize the manufacturing process – reducing NMP use, improving recovery, and minimizing environmental impact and costs.
Contact Vaisala today to find out how inline refractometers could reduce your costs and improve the sustainability of your operations.
More on the topic
Polaris Process Refractometer PR53GP
Measure NMP chemical concentrations directly in pipelines and tanks.

Accurate moisture and concentration measurements in battery manufacturing
Protect your dry room with fast-response, accurate monitor and control devices, and equip your dehumidifier unit and critical process steps—such as anode and cathode drying, solvents, glove boxes, and other inert atmospheres—with products engineered for the most demanding environments.
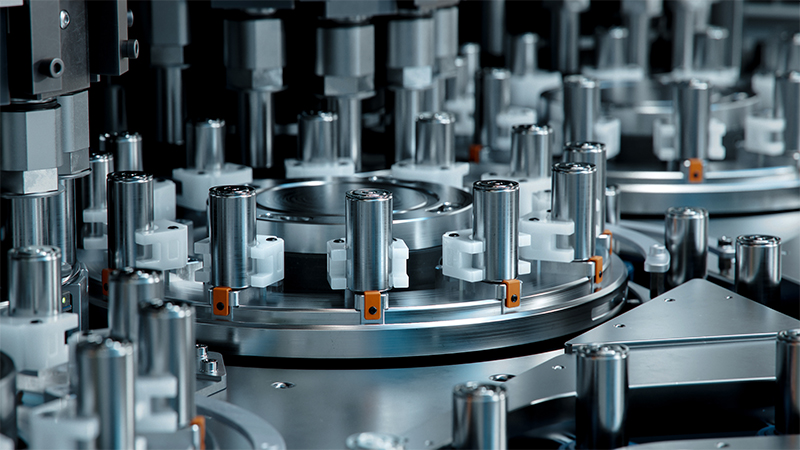
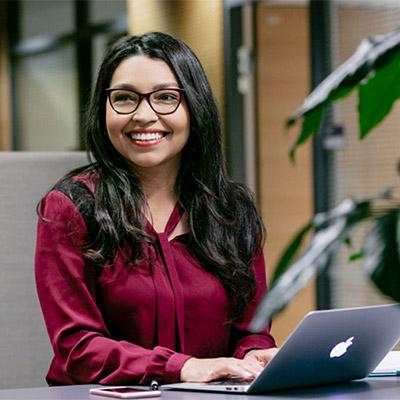
Contact us
Interested to receive more information on a specific application or product? Drop us a line, and we'll get back to you!